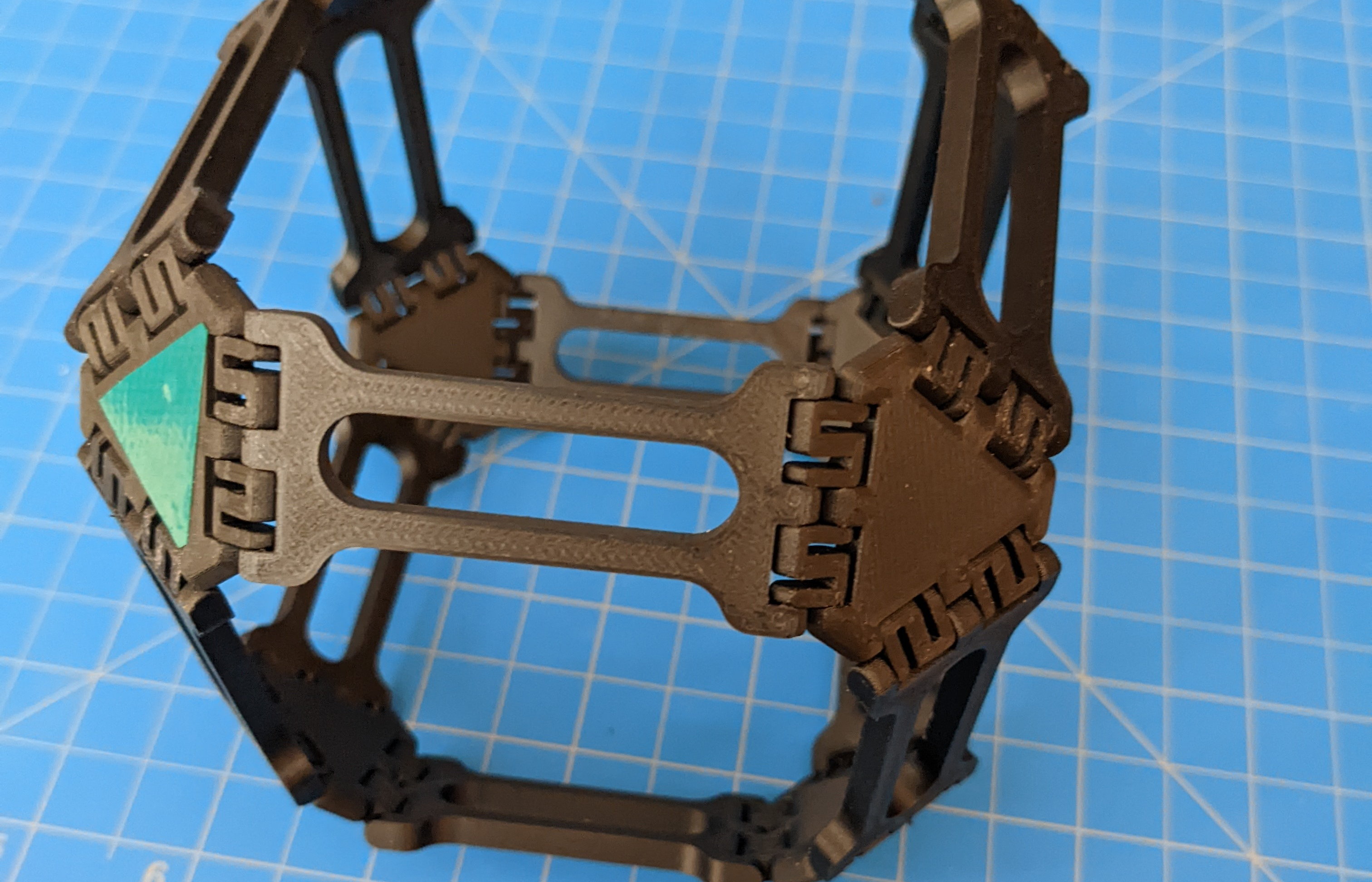
Auxetics and Foams
I spent the summer of 2022 working at CSAIL (Computer Science and Artificial Intelligence Lab, MIT) participating in researching auxetics of various designs and testing the material properties of celled “foams”.
Project 1: Handed Shearing Auxetics
This project dealt with flattened shapes which expand diagonally on living hinges. I used the Rhino + Grasshopper design programs to change the parameters of the living hinges and printed them out of FPU on a resin printer, then tested each design to determine which set of parameters best contributed to the expansion of the auxetic shapes.
The shapes were tested on a mechanical testing rig that I designed, built and programmed with Arduino to repeatedly stretch the shapes.
Project 2: Flipping Shapes
Regular polyhedra each have duals. It’s possible to connect the vertices of a polyhedron to the vertices of its dual in such a way that the shape can be “flipped inside-out”, which has been put to use in color-flipping toys such as the Hoberman Flip Out.
This project reconstructed a tetrahedron-tetrahedron flipping shape, as well as a cube-octohedron one, in order to investigate possible methods of actuation.
I designed the hinge and vertex system for this shape, which scales to the cube-octohedron shape as well, in Solidworks before printing it in a combination of FDM and SLA parts.
Project 3: Foams
There’s continual research into the use of different materials, or differently arranged materials, for use in the bodies of soft robots. In this case, my lab was testing different parameters, such as cell density and chord thickness, of structures called “foams” which were printed from a highly elastic rubber material.
I printed the foams from EPU on a resin printer, then designed and ran tests to determine their material properties.